Reducing Belt Damage
It is safe to say that conveyor belts are the most important and expensive function in a conveyor system – they provide a rapid and safe method of moving large quantities of materials from one location to another. In the Quarry industry, conveyor belt systems are used continuously. Quite often maintenance specialists find themselves looking into how to effectively minimise impact damage, reduce maintenance costs, whilst also increasing plant productivity. Belt damage at the primary crusher is often of concern. This can be caused by a number of reasons, such as:
- type, size, and shape of the rock
- weather conditions e.g. some types of rock, when wet, cut the rubber belt more efficiently
- belt speed
- belt width
- freefall height
- poor design height and space from the underside of the jaw conveyor
- type of belt support e.g. standard or impact idlers.
This information is common knowledge and has been addressed in the past by the following:
- wide heavy duty belts, running at slow speeds often short in design and transferring onto another narrower belt running at a high speed for delivery to surge pile or secondary crusher
- applying scalped fines to the belt providing protection to the belt cover
- fitting of static impact beds e.g. rubber bars in a cradle.
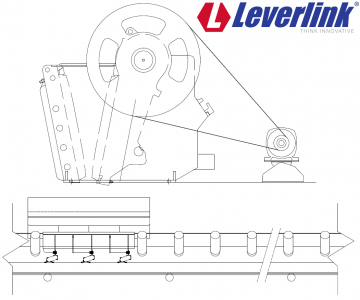
(fig. 1 Sketch of a Jaw Crusher)
This dissipation of kinetic energy at belt loading point and continual improvement programs have been our passion for almost 30 years. Leverlink’s Dynamic Impact Bed for conveyors has proven its worth and ongoing benefits in both quarrying and heavy mining applications.
Case Study
We had a customer contact us recently, requesting we provide a solution to the problem of continually changing out rollers at a transfer point that was difficult to access and maintain. There was minimal impact but high cost due to confined space and a crane being required. We supplied a very light duty system and sized the slide media for change out at approximately every 5 years. We monitor slide media wear to maintain ongoing maintenance awareness. Written by Richard Sharp, Managing Director- Leverlink