Heavy Duty Adjustable Motor Base
Leverlink proudly stands as Australia’s top manufacturer of stored energy motor bases (also known as self-tensioning, tensioning, or auto-tensioning motor bases). Our adjustable motor base plates cater to both electric and combustion motors, offering versatility for diverse applications.
At the core of these bases lies a rubber torsional spring. This innovative component provides consistent force, automatically compensating for belt stretch and wear. The intelligent mechanical design facilitates quick belt installation and replacement, requiring only a single adjusting screw. This translates to enhanced safety and minimised risk of injury.
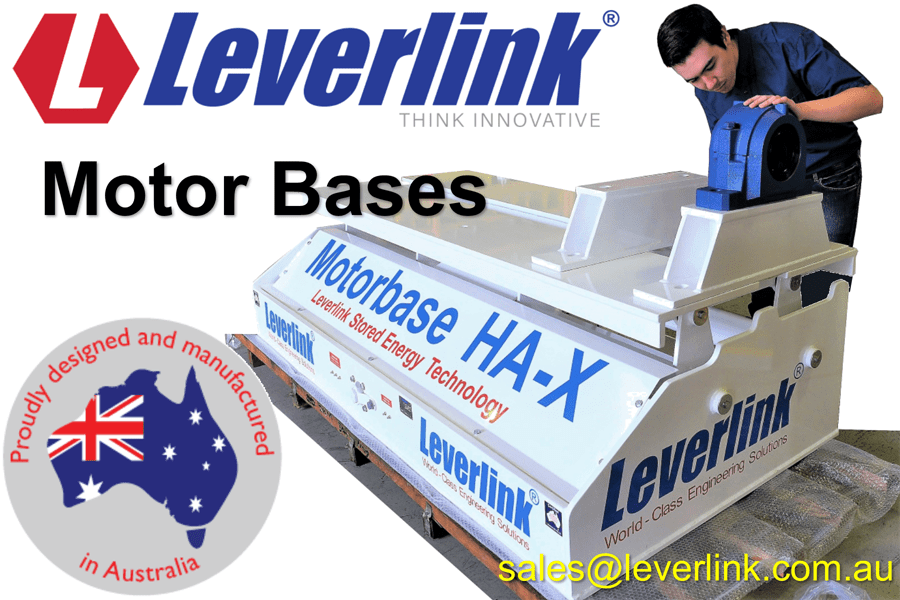
Applications:
- Slurry Pumps
- Sump Pumps & Other Pumps
- Crushers
- Vibrating Screeners
- Feeders
- Grizzlys
- Various Quarry & Mining Applications
Why Leverlink
- Designing and manufacturing motor bases for more than 20 years
- Custom options
- Proven in the most hostile environments
- Increases safety, lowers personal injury risk
Contact our knowledgeable team today to discuss your specific needs and discover how our motor bases can elevate your operations!
Motor Base Categories
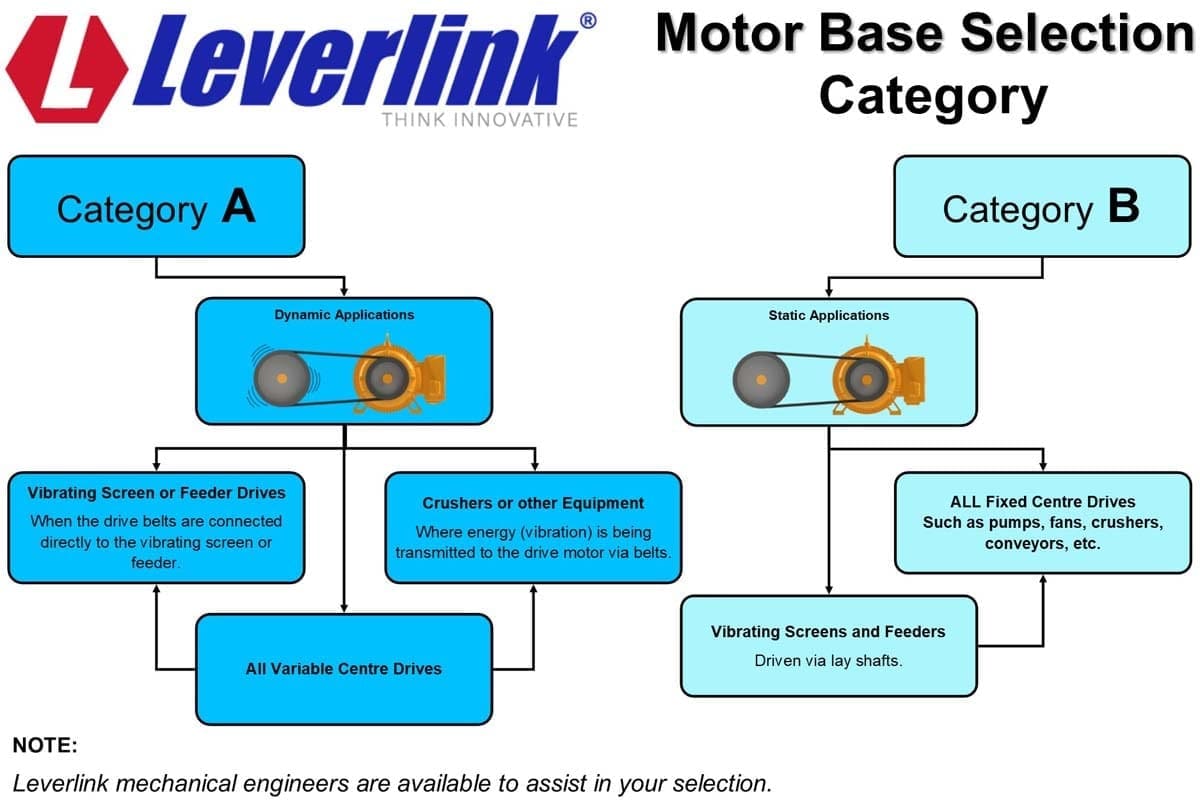
Category A – Dynamic Applications
Vibrating Screen or Feeder Drives
When the drive belts are connected directly to the vibrating screen or feeder.
Crushers or other Equipment
Where energy (vibration) is being transmitted to the drive motor via belts.
All variable Centre Drives
Category B – Static Applications
All Fixed Centre Drives
Such as pumps, fans, crushers, conveyors, etc.
Vibrating Screens and Feeders
Driven via lay shafts.
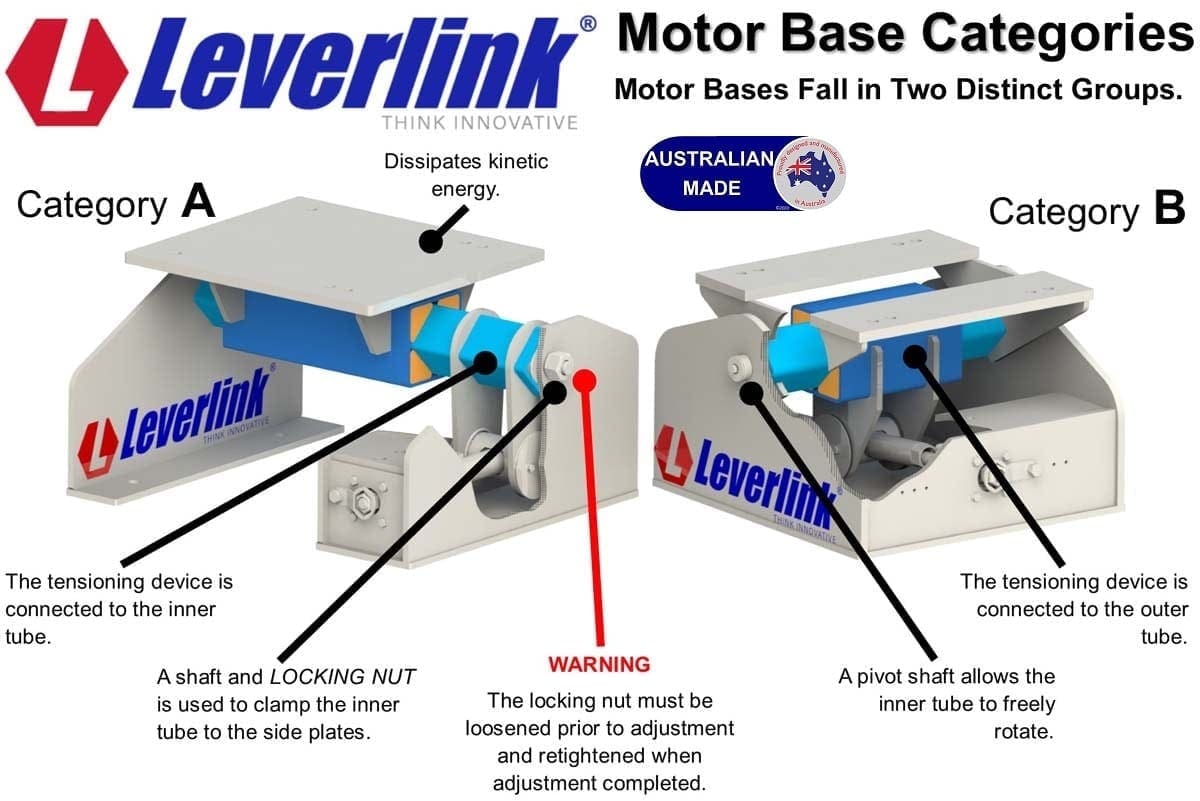
Category A
- The tensioning device is connected to the inner tube.
- A shaft and locking nut is used to clamp the inner tube to the side plates.
Warning: the locking nut must be loosened prior to adjustment and tightened when adjustment completed.
Category B
- A pivot shaft allows the inner tube to freely rotate.
- The tensioning device is connected to the outer tube.
Motor Base Categories
Leverlink designs Motor Bases for Crushers Drives to simplify the installation, tensioning,checking and re-tensioning of the V belts. Leverlink technology is innovative and uncomplicated. Tried and proven in the harsh environments of mining and quarrying for more than 30 years. The principal of the system is to utilise a rubber torsion spring to store energy.
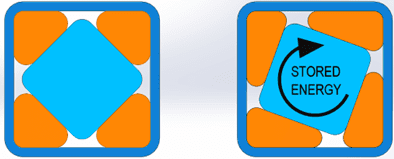
- The rubber torsion spring is mechanically loaded against the ve belts until the belt manufactures maximum specified tension is achieved.
- The stored energy in the spring will compensate for belt stretch and wear but should be checked periodically to ensure but tension does not fall below manufacturers minimum tension specification.
- The amount of available take up or compensation is variable due to mechanical factors such as moment arm lengths, angle of spring compression required to tension belts.
Application Note: Self tensioning, self adjusting and tensioning are marketing terms used by various manufacturers.
Single Tensioning Device
Secondly, the single Tensioning Device is sealed and lubricated. Remote grease lines are often used for ease of maintenance.
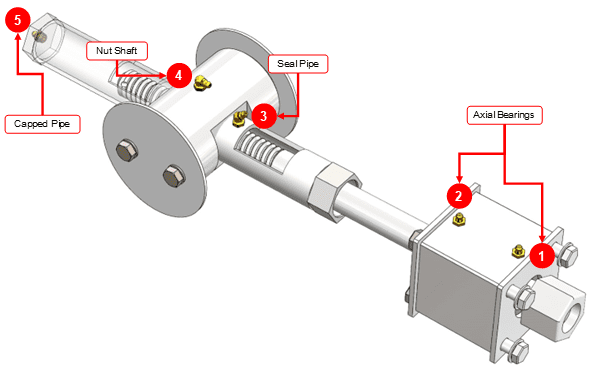
Example of HAQ Series
A rugged frame provides enclosure for all working components and allows the electric motor to be fixed in place.
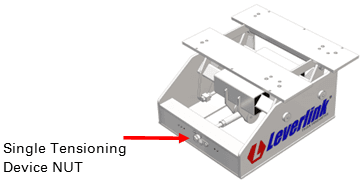
What type of crusher is best?
Crusher drives come in a wide range of designs and sizes as do crushers. Some typical crushers are used in mining, quarrying, recycling and other associated industries.
For example:
- Jaw Crushers (Single & Double toggle)
- VSI-Vertical Shaft Impactors
- Hammer Mills
- Cage Mills
- Gyratory and Cone crushers
- Rolls crushers
- Sizers
In mining and quarrying, these In mining and quarrying, these would perform applications such as primary, secondary
and tertiary crushing. Typically, these would be belt driven.
Jaw Crusher with LEVERLINK Motor Base
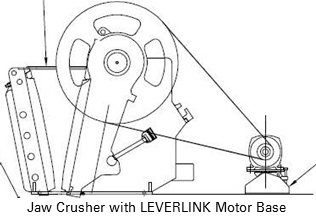
Typical LEVERLINK VSI Drive arrangement
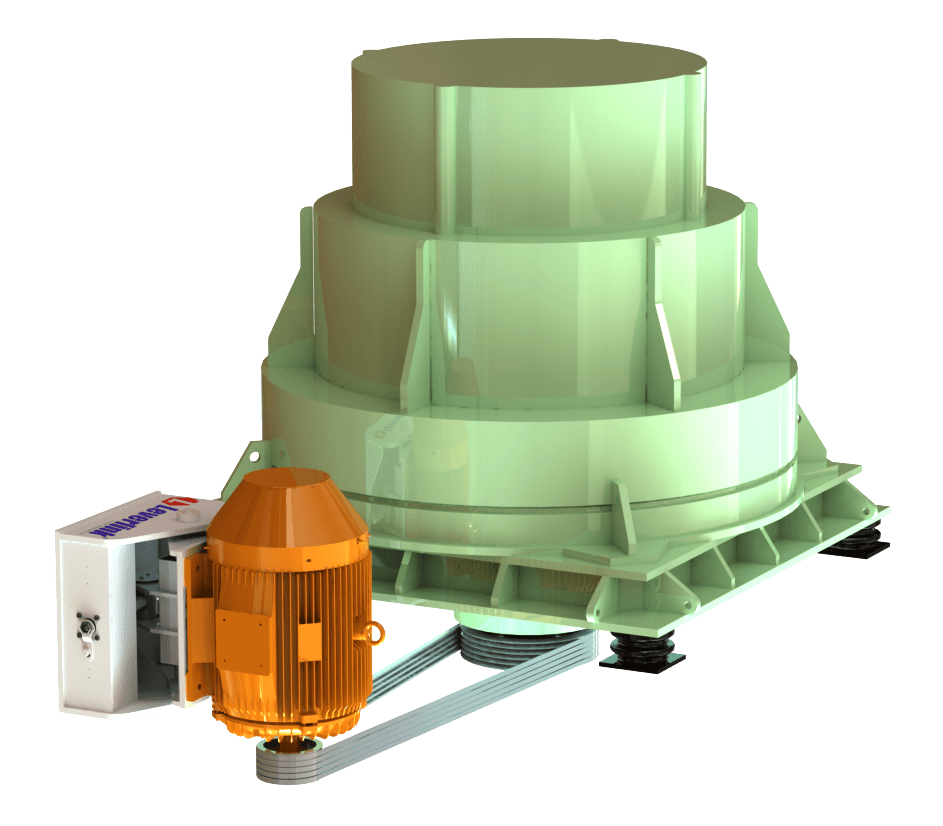
Crusher Drive Arrangement
Small to medium size crushers, say up to 400kW, would be driven directly off the motor shaft. However, larger electric motors, say +/- 1000kW range would utilise a lay or jack shaft coupled directly to the motor to transfer the forces to a inboard or outboard drive pulley.
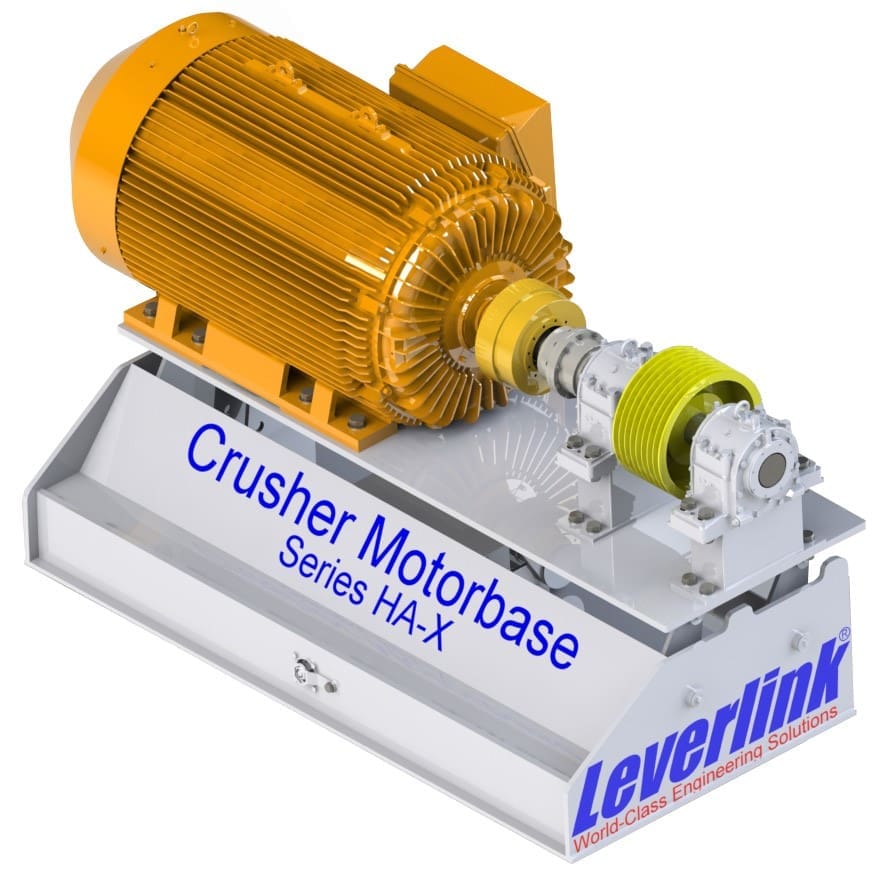
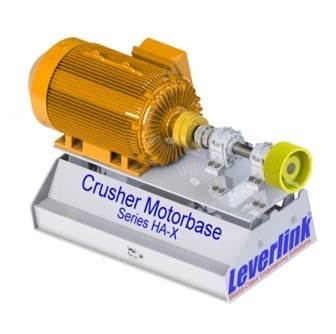
Crusher Slide Rails and Base Frame
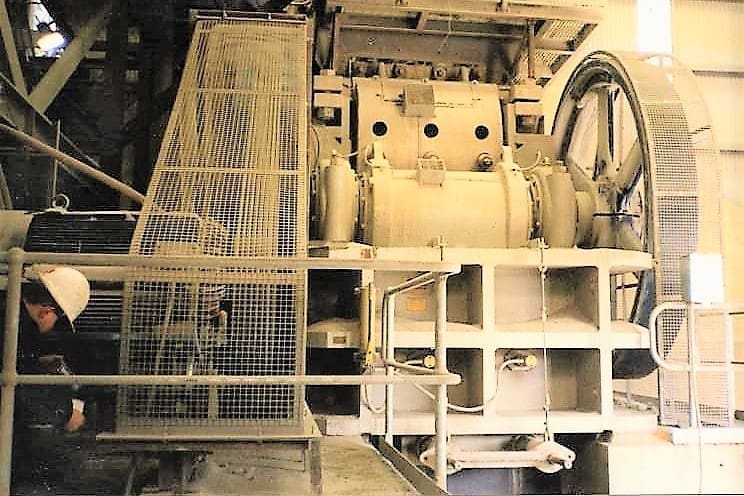
The electric motor would be connected to some form of system to allow the tensioning of the belts. In larger motor sizes with jack or layshaft drives it was not uncommon to fix the drive centers and employ a jockey pulley on the back of the drive belts as a means of tension.
What are the symptoms of a bad driver belt?

It has been our experience that poor drive belt maintenance often reflects the difficulty of the adjusting system to perform the task.
These may be:
- Corroded adjusted screw
- Difficult to access adjusting mechanism.
- Alignment-No means of facing drive and driven pulleys.
- Poor guarding design resulting in difficult access to check and or adjust drive belt tension.
- Poor or no job training.
Misalignment of drive and driven pulleys will shorten V-belt life and cause costly pulley wear.
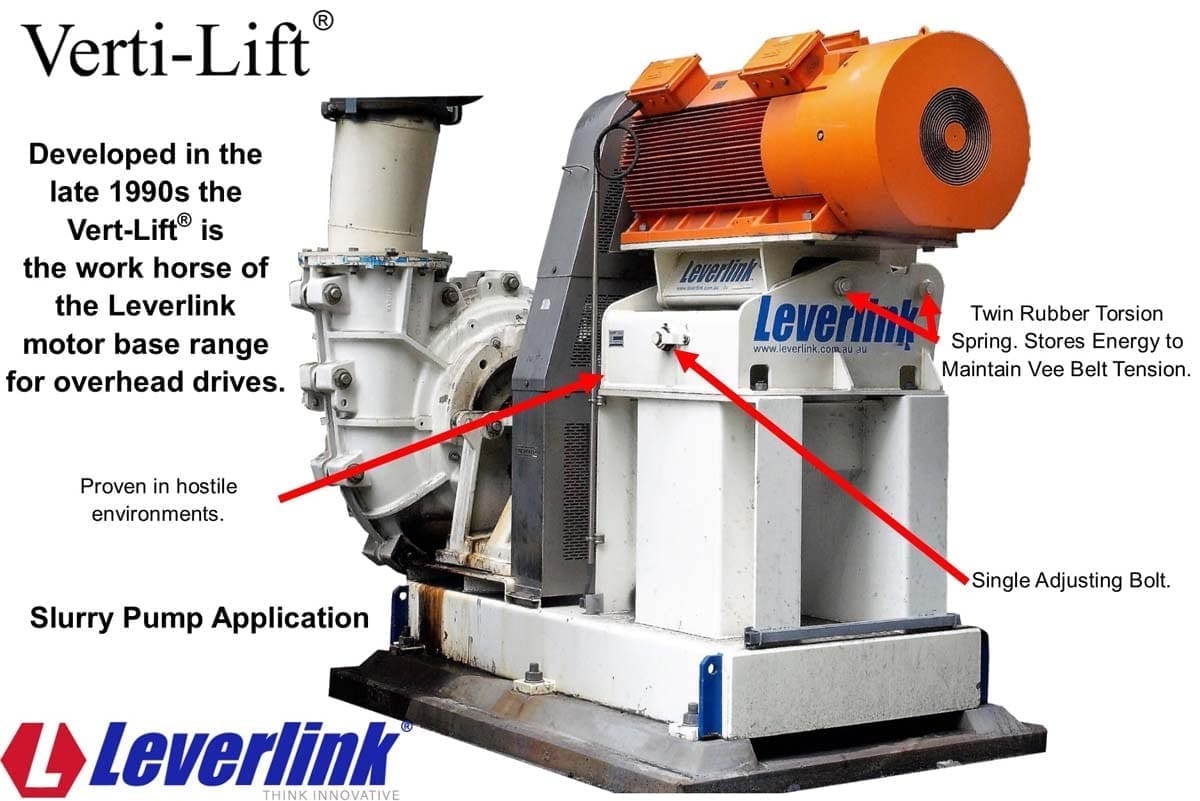
Overhead Drive Motor Bases
Developed in the mid 1990s the Vert-Lift® is the work horse of the Leverlink motor base range.
- Proven in hostile environments
- Single adjusting bolt
- Twin rubber torsion spring stores energy to maintain Vee belt tension
- Single adjusting bolt
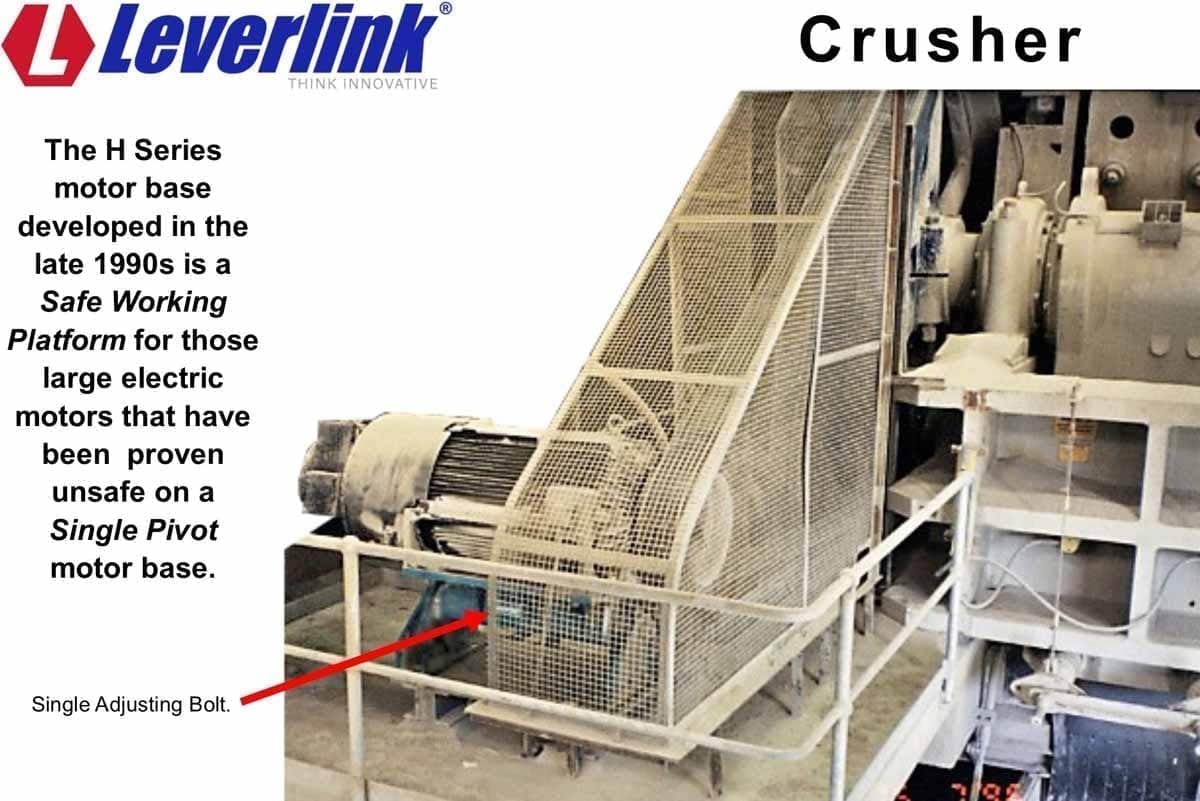
Horizontal Drive Motor Bases
The H Series motor base developed in the late 1990’s is a Safe Working Platform for those large electric motors that have been proven unsafe on a Single Pivot motor base. Features a single adjusting bolt.
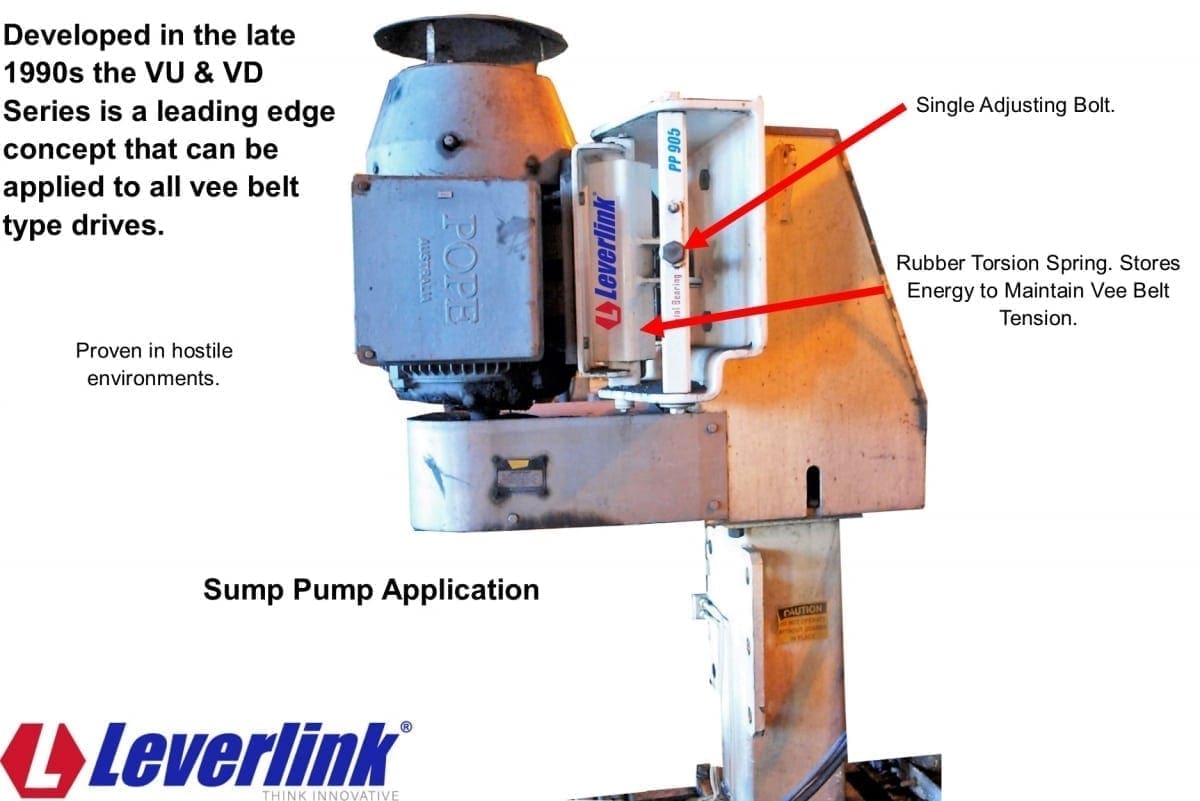
Vertical Drive Motor Bases
Developed in the late 1990’s the VU and VD Series is a leading edge concept that can be applied to all Vee Belt type drives.
- Proven in hostile environments
- Single Adjusting bolt
- Rubber torsion spring stores energy to maintain Vee Belt Tension
Request a quote
To request a quote or find out more information, please complete the form below or call us on +617 3737 2400.
Products
- Spray Bars for Vibrating Screen Washing
- V Belt Tension Gauges
- Lever Springs for Vibrating Screens and Feeders
- Pump Drives & Machine Base Frames
- Conveyor Dust Enclosures
- Conveyor Belt Edge Supports
- Conveyor Wear Plates
- Motor Support Structures for Vibrating Screens
- Heavy Duty Industrial Chain Tensioner
- V Belt Tensioner & Jockey Tensioner - Stored Energy
- Rubber Torsion Springs & Rubber Suspension
- Dynamic Conveyor Impact Bed
- Heavy Duty Adjustable Motor Base
- Machine Guarding for Conveyors, Pumps & More
View products
Services
Recent articles
- Leverlinks revolutionary Dynamic Impact Bed for Conveyors23 April 2025 - 11:32 am
- Everything you need to know about waterjet cutting16 June 2024 - 6:00 am
- 4 Ways to Reduce Conveyor Belt Damage2 December 2022 - 11:19 am
- Best Conveyor Wear Plates in 20228 September 2022 - 6:00 am
Contact us
Phone +617 3737 2400
Send us an email
24 Meadow Avenue
Coopers Plains, QLD 4108