Dynamic Impact Bed for Conveyor Load Zones
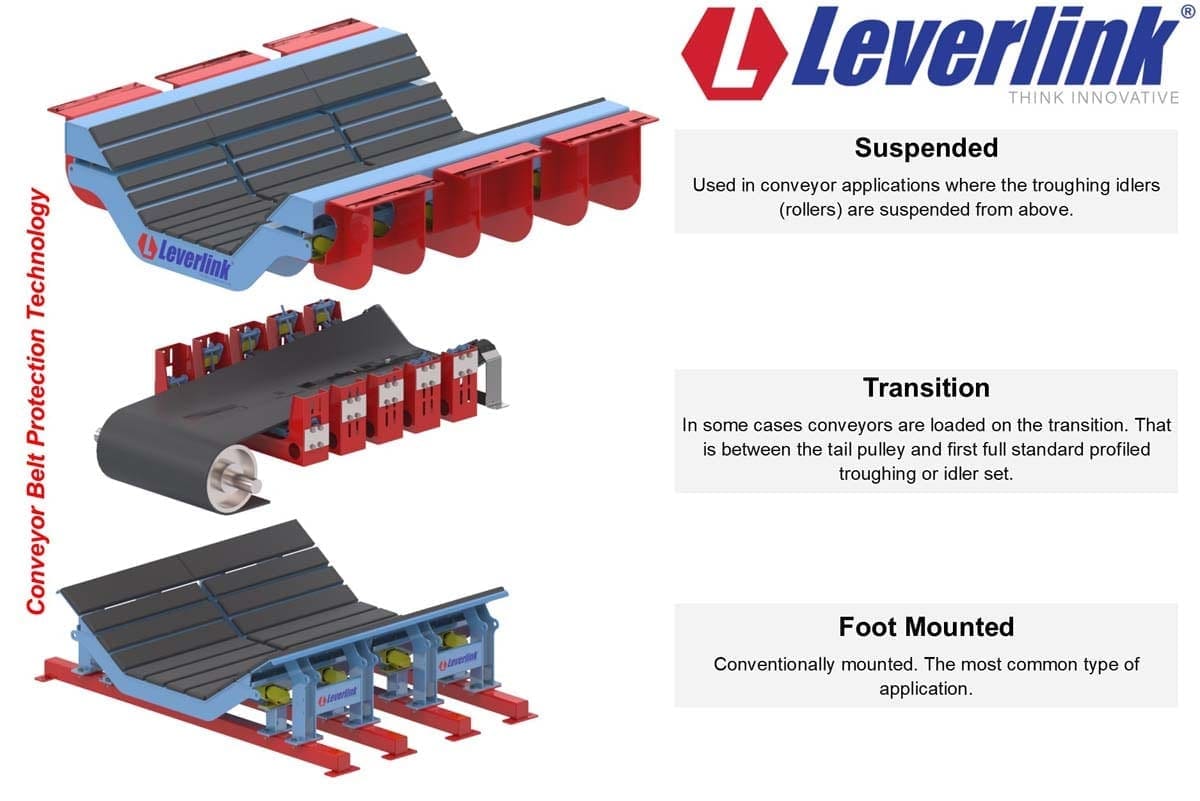
- Individually designed and engineered for your application
- Dissipates kinetic energy
- Specialising in big belts (1200mm to 3000mm wide)
ROM LOAD ZONE UPGRADE REMEMBERED
Towards the end of 1993, A major mining operation requested Leverlink investigate the ROM conveyor load zone as high belt wear, impact roller failure and spillage was a major concern.
Intelligence gained from a site visit determined two large feeders discharging at 90° onto a common 1600 wide conveyor belt supported by suspended or garland type toughing rollers. The feed was not centred on the belt and made for tracking and spillage problems.
Leverlink proposed 3 major design changes:
- Remove the suspended (garland) toughing sets and replace them with Leverlink Dynamic Impact Beds at the discharge zones of the feeders and foot mounted troughing sets in rest of the load zone.
- Install a Dynamic Impact Plate (adjustable toe) opposite each feeder to centre the feed on the conveyor belt.
- Rebuild the dust enclosures to control spillage and air borne particles.
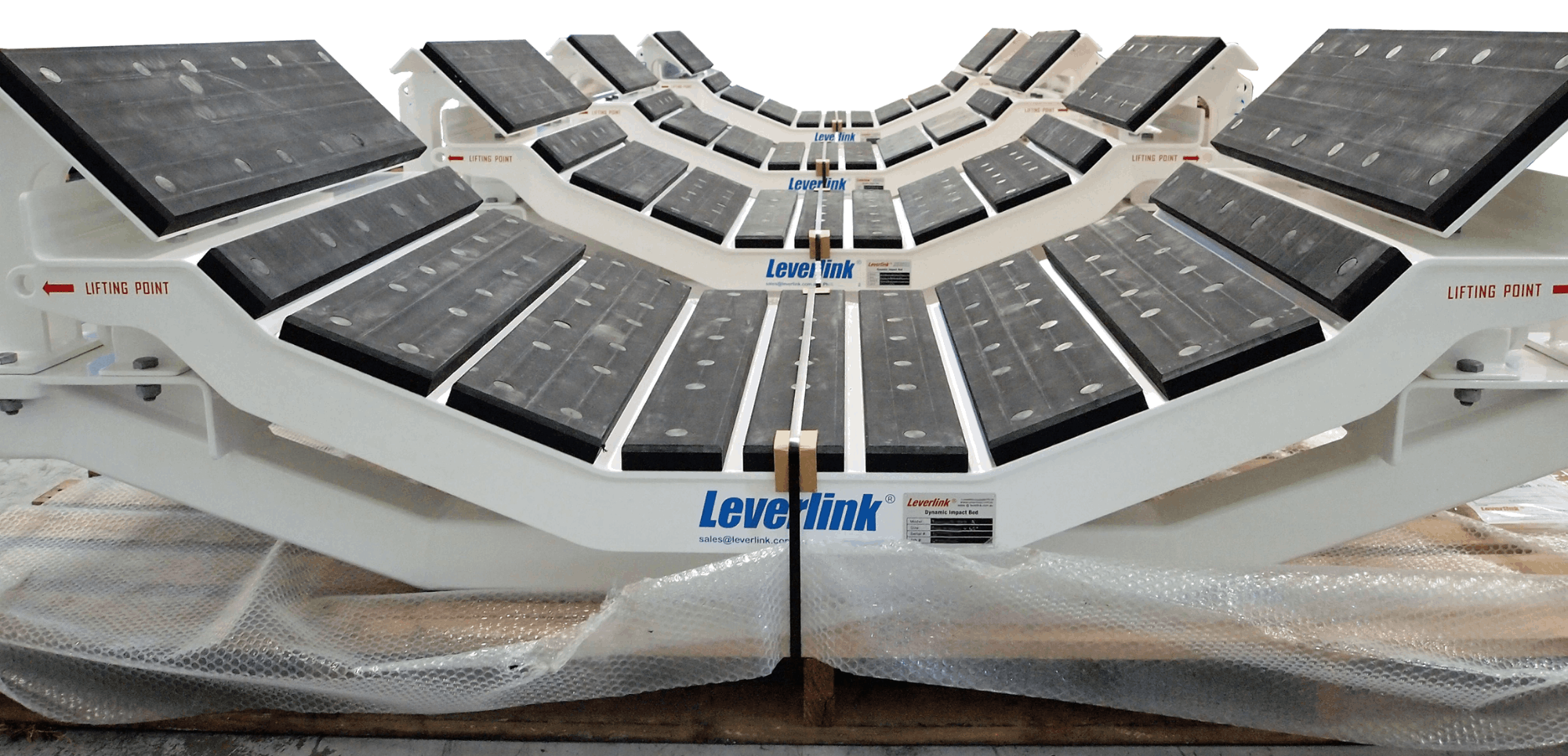
Dissipation of Kinetic Engery
It was conceived from an idea to develop a better and more reliable product; one that would dissipate kinetic energy and provide the benefits of long service life, as well as assisting in reducing maintenance costs in terms of consumables and labour.
In Continuous Production for more than 30 years – using rubber torsion springs as suspension was radically different from the static impact beds that were previously dominating the Australian marketplace.
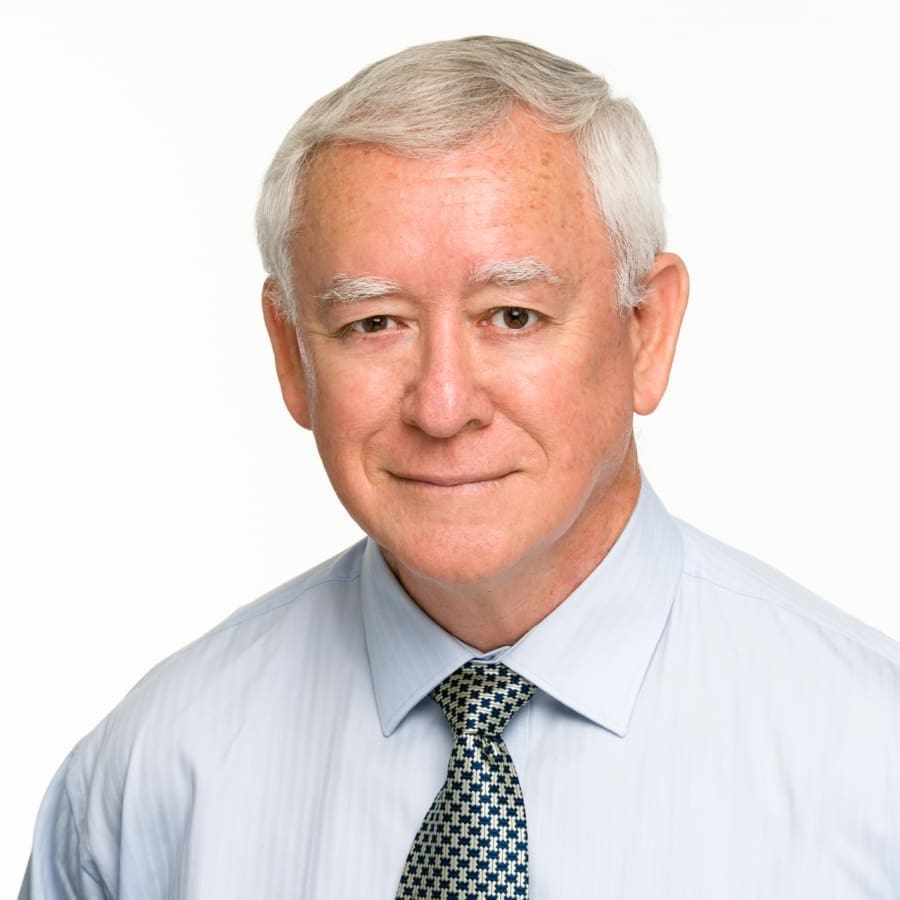
- Dissipate Kinetic Energy
- Reliability and Long Service Life
- Reduce Consumable and Labour Costs
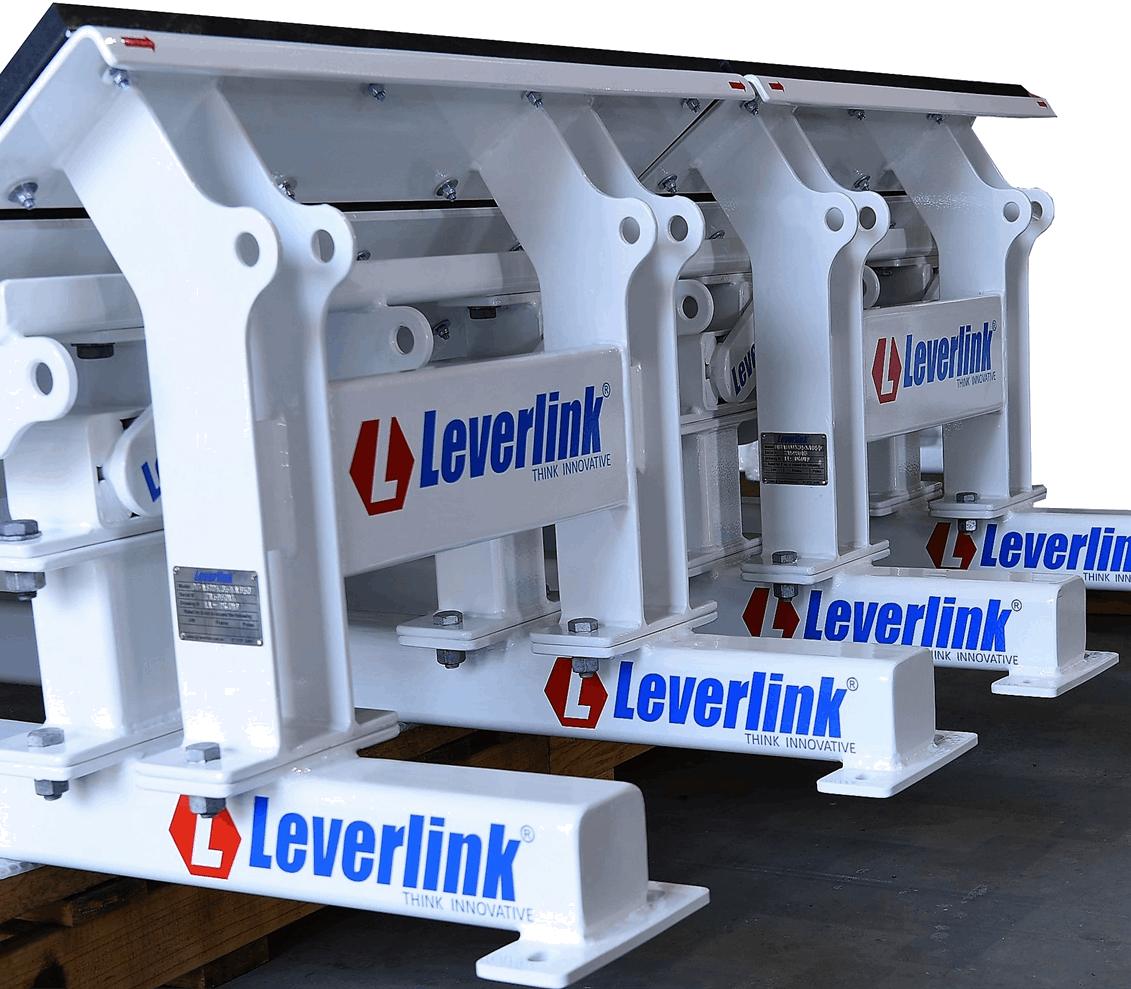
Multiple Trough Impact Systems
More than 30 years of engineering and applying the Leverlink Impact Technology in the harshest of mining applications has proven the Leverlink multi-trough system will reduce maintenance costs, provide a long service life and will not fail.
Custom designed and engineered in-house

The Customer Agreed With Our Design
RESULTS
The belt now tracked correctly due to:
- Dynamic Impact beds and foot mounted troughing roller sets stabilized the belt.
- The Dynamic Impact Plate (adjustable) placed the material in the centre of the belt and eliminated the tracking problem. Impact energy was dissipated via the rubber impact mounts.
Roller damaged was eliminated:
- The Dynamic Impact Beds absorbed and dissipated the impact energy. It also protected the supporting structure.
Belt Damaged Reduced:
- Damage to the belt was reduced noticeably.
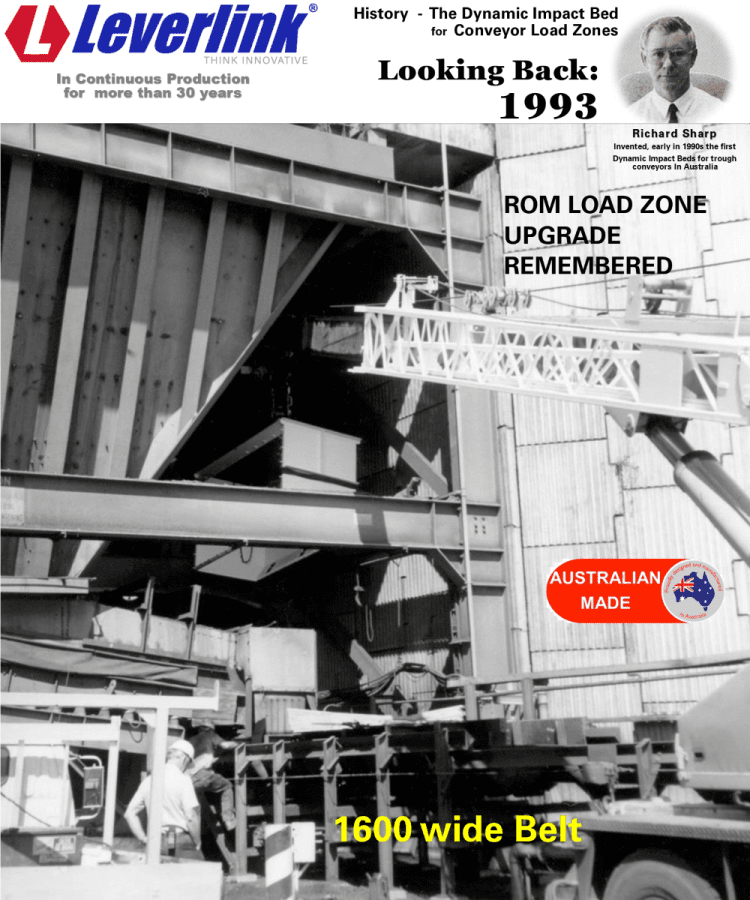
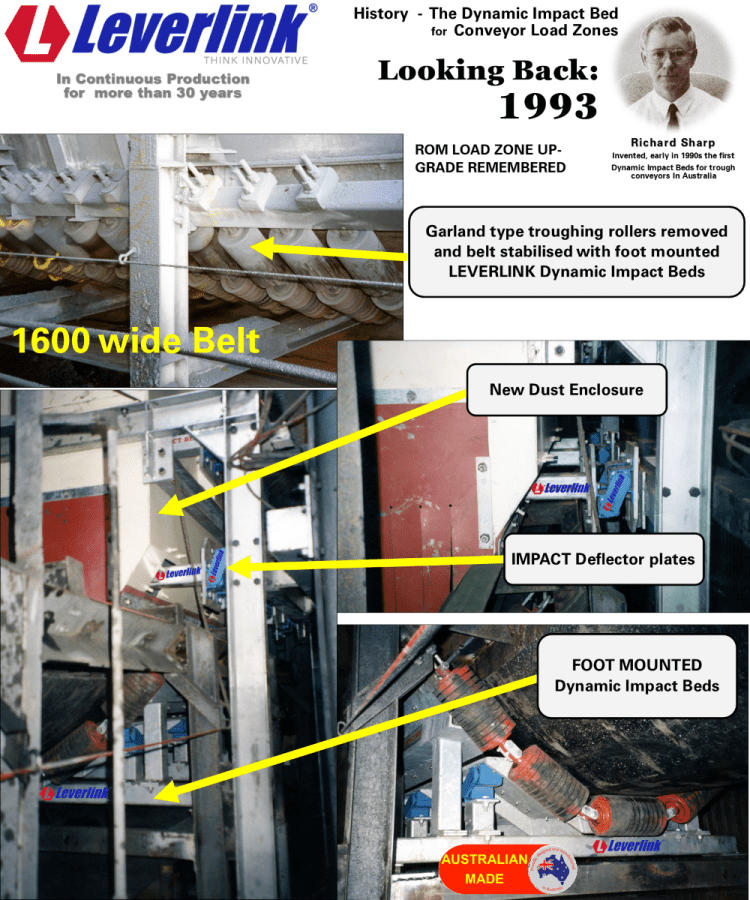
Leaders in Dynamic Impact Beds
Leverlinks Dynamic Impact Beds are custom-built to your site requirements. We engineer our Dynamic Impact beds with an emphasis on structural integrity, belt preservation, and leakage prevention.
Designed to your application – We design with cost-effective methods in order to increase belt life and reduce maintenance time.
Dynamic Suspension System – Dissipates kinetic energy to protect belts and structure of the conveyor systems.
Fixed Wings to prevent leakage – This method reduces wastage and minimises clean up while also assisting in eliminating WHS issues.
Polymer Slider Bar Media – Available in FRAS. No rollers to fail due to impact.
Protective Coating – Our protective coating has proven to last over time, even in the harshest environments.
Conveyor belt protection technology
- Suspended – used in conveyor applications where troughing idlers (rollers) are suspended from above.
- Transition – In some cases conveyors are loaded on the transition. The is between the tail pulley and first full standard profiled troughing or idler set
- Foot mounted – Conventionally mounted—the most common type of application.
Specifications and guidelines
We design the Dynamic Impact Beds to minimise the current problem and maximise service life. Should your application exceed the specifications provided in this brochure please contact us. All beds are custom designed and engineered to suit your application.
Impact Speed | Impact bar material | Tonnage per hour |
---|---|---|
Up to 6 m/sec | Polymer Slide Media, FRAS available | Up to 15,000 tph |
Available size | Maxium temperature | Impact Energy |
---|---|---|
Up to 3000mm belt width | Polymer -150°C to 80°C | Lump weight: 500kg |
Length to suit | FRAS -250°C to 80°C | Drop height: Up to 10 metres |
Leverlink Skirting Systems
It is best to combine Leverlink’s Dynamic Impact Bed with Leverlink’s Skirting Systems to minimise leakage and reduce maintenance. Please contact us in regards to our Skirting Systems in order to provide you with the most accurate information.
Benefits of Leverlink’s innovative impact mount
- No rollers to replace
- Minimises belt and structural damage
- Cost-effective
- Ten-year structural and mechanical warranty
Downloads
Request a quote
To request a quote or find out more information, please complete the form below or call us on +617 3737 2400.
Products
- Spray Bars for Vibrating Screen Washing
- V Belt Tension Gauges
- Lever Springs for Vibrating Screens and Feeders
- Pump Drives & Machine Base Frames
- Conveyor Dust Enclosures
- Conveyor Belt Edge Supports
- Conveyor Wear Plates
- Motor Support Structures for Vibrating Screens
- Heavy Duty Industrial Chain Tensioner
- V Belt Tensioner & Jockey Tensioner - Stored Energy
- Rubber Torsion Springs & Rubber Suspension
- Dynamic Conveyor Impact Bed
- Heavy Duty Adjustable Motor Base
- Machine Guarding for Conveyors, Pumps & More
View products
Services
Recent articles
- Leverlinks revolutionary Dynamic Impact Bed for Conveyors23 April 2025 - 11:32 am
- Everything you need to know about waterjet cutting16 June 2024 - 6:00 am
- 4 Ways to Reduce Conveyor Belt Damage2 December 2022 - 11:19 am
- Best Conveyor Wear Plates in 20228 September 2022 - 6:00 am
Contact us
Phone +617 3737 2400
Send us an email
24 Meadow Avenue
Coopers Plains, QLD 4108